Panther Partner Spotlight Rani ElHajjar: Championing Integrity & Reliability of Composites
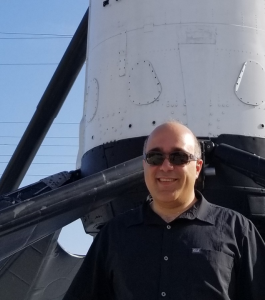
by Brian Walsh
Expertise Highlights: How can Rani help you? Field of Interest: Polymer-Based Composites: Defect analysis and development of new structural materials Experimental Mechanics: Composites, Smart materials, Defects, Fracture Mechanics, Effects of defects in composite structures Full Field Non-Destructive Testing Methods Testing Composite Structures for Safety Developing Composite Materials for Zero Greenhouse Emissions
Skills: Mechanical behavior of materials Mechanical testing Mechanics of materials, composite materials Computational structural, Fracture & Damage, Experimental mechanics Stress, fracture & failure analysis Structural engineering Composite structures Multiscale modeling Laminated composites Composite cure simulation
Partnering Ideas: Improve build reliability on composite fabricated parts to reduce failure risk Characterize new composite parts or structures at multiple scales, from fiber and matrix up to the structural level components Resources for Partnering: Hardware: Composite fabrication, Environmental testing, Digital image correlation, Acoustic emission, Strain measurements, Mechanical testing Software: Cure simulation, Matlab, Mathematica, ANSYS
Tell us about your main area of expertise.
My recent areas of focus are in nondestructive full field analysis of strain and stress in polymer-based composite materials. These materials are becoming increasingly popular across various industries due to their lightweight nature, corrosion resistance, and cost-effective manufacturing. However, the complexity and variability in the manufacturing process of polymer composites can lead to reliability issues in the final structure compared to traditional materials like metals. Thus, there is a need to consider how the manufacturing interacts with the final structure’s performance.
My work also involves using advanced full field measurement techniques, which offer a comprehensive view of strain and stress distribution across the entire material. This approach helps identify discrepancies between expected and actual performance, guiding necessary adjustments in the manufacturing process or design to prevent failures.
What are some ways you and UWM can help companies?
I am often called upon to help companies manage the complexities of composite materials testing as they relate to production challenges. Many companies face difficulties in conducting specialized tests and navigating the extensive array of testing requirements, particularly if they have limited R&D capabilities.
At UWM, we provide access to specialized testing techniques and fixtures recommended by ASTM and ISO standards for comprehensive testing and characterization. We also have the unique capability to both make composites and subject them to rigorous destructive and non-destructive testing across various environmental conditions. This integrated approach allows us not only to help companies assess the performance and durability of their materials but also to optimize production processes and mitigate potential issues early on.
Give us a few examples of how you have helped companies in the past.
I’ve had the opportunity to work with various companies, both large and small, on fascinating projects involving composite materials. My research expertise in the areas above is well captured in a recent book we published with Wiley titled Composites Structures: Effects of Defects, which has been well-received and is widely used by industry professionals.
At SpaceX, for instance, I was directly involved in the build reliability and engineering of composite spacecraft parts they manufacture. In my contribution, I set up documentation and processes to control and assess the severity of manufacturing anomalies and helped manage deviation scenarios. We conducted extensive testing to understand how different types of defects or manufacturing anomalies affected the structural properties of composite materials, which are inherently more variable than metals.
Another significant project was with Boeing before I joined UWM, where I was part of the team involved in the certification process for the 787 aircraft. The 787 marked a major shift by incorporating a substantial percentage of composite materials in its primary structure, including the wings and fuselage. This was considered risky by some but a necessary innovation to stay competitive in the future. Our team focused on identifying and evaluating manufacturing defects and processing anomalies to ensure they were accounted for in the design. Despite the challenges Boeing has faced, our work contributed to their understanding and management of composite material risks.
I also collaborated with Hyundai, where I hosted and advised a representative from the company at UWM. He spent a year prototyping various mechanical parts using full field strain analysis methods. We selected a specific part – a bracket in one of their heavy vehicles – and compared the original and improved version when a new welding scheme was implemented and assessed stress distribution to enhance its performance. This collaboration was structured similarly to a graduate research project, culminating in presentations and a final report to Hyundai.
Additionally, I worked with a startup company in Superior, WI, that aimed to build a small airplane using sandwich structures. Despite the company’s financial challenges, we assisted them with material testing and characterization at UWM, providing valuable insights for their development process.
Is there a specific sector you would like to work with?
Aerospace is always interesting. I would love to get more involved with electric vertical take-off and landing (eVTOL) aircraft – the kind that fly short hops solely on electric power. I think they will be game-changers in the near future, and I’m pretty sure the structure has to be composite to be able to compete. There are already many startups exploring these airplanes in the field. I think my lab at UWM can help them because we have the fixtures for testing and the know-how to give them a leg up on their certification process.
Can you tell us one fun fact about your personally or professionally?
I’ve recently been exploring the concept of risk analysis. Inspired by recent rare events like the pandemic or market crashes that were believed to be outliers. I’ve delved into understanding how to manage and design unexpected and extreme events that fall outside typical expectations. Many of our current design processes assume normal distributions of material and structure properties, but there are often unpredictable “tail risks” that can impact materials and processes, especially in newer technologies like polymer-based composites where there are many moving parts. I’m actively researching ways to integrate these insights into our approach to designing and utilizing these materials, aiming to mitigate and manage risks effectively.
Brian Walsh is a Senior Technology Commercialization Manager of the UWM Research Foundation whose mission is to guide innovation, ignite startups, and foster partnerships with companies worldwide. Walsh joined the UWMRF in 2022 and has helped to grow the organization and build new programs to support UW-Milwaukee’s cutting-edge researchers and new entrepreneurs.